Quality Testing
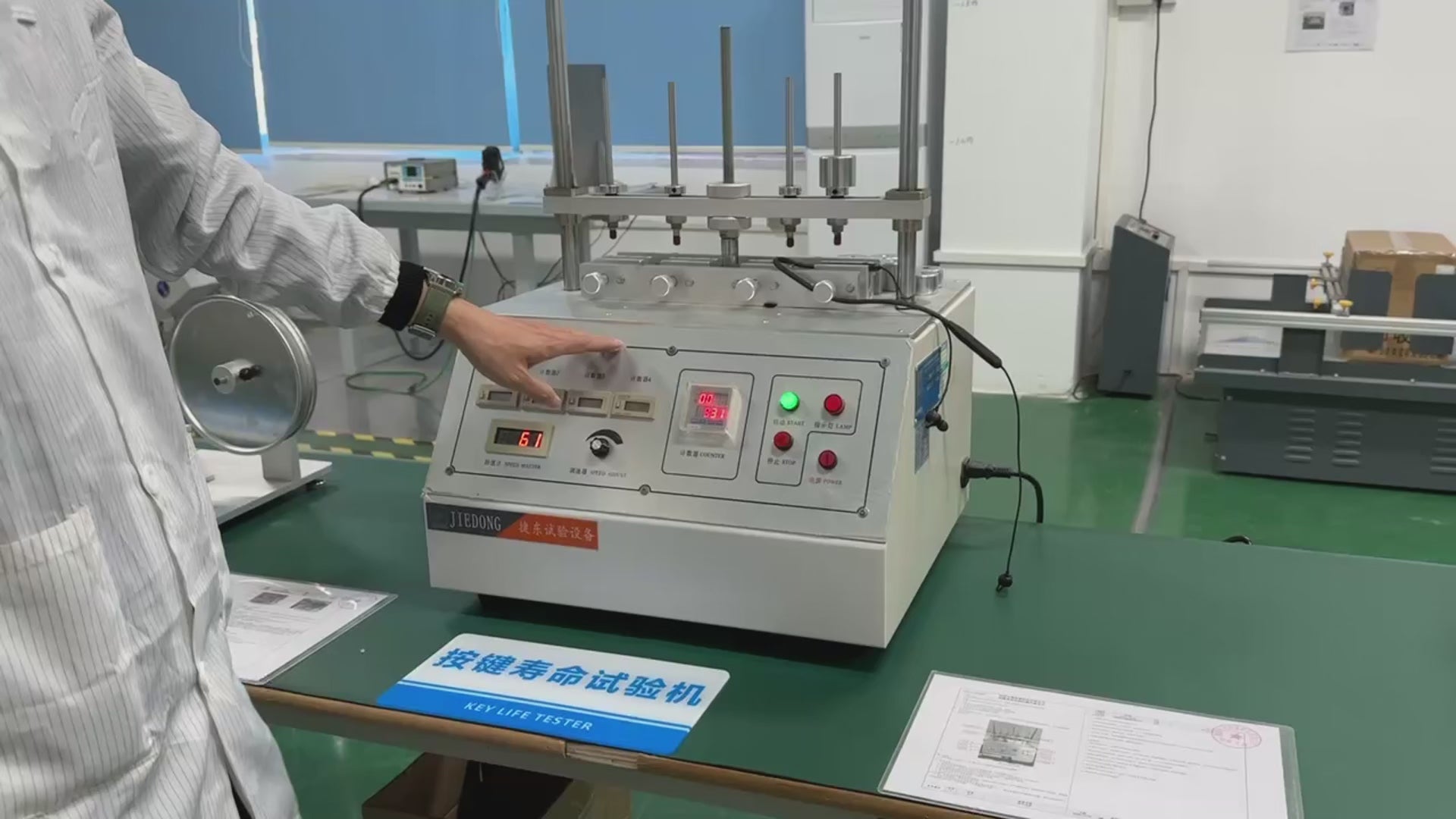
Key Lifecycle Test Machine
This is our key lifespan testing device. During the testing process, we use the device's impact head to repeatedly press the key, simulating real user scenarios. The test consists of 30,000 presses. After completing the test, we evaluate the key's functionality to ensure it responds correctly and that its electrical performance remains stable and free of abnormalities.
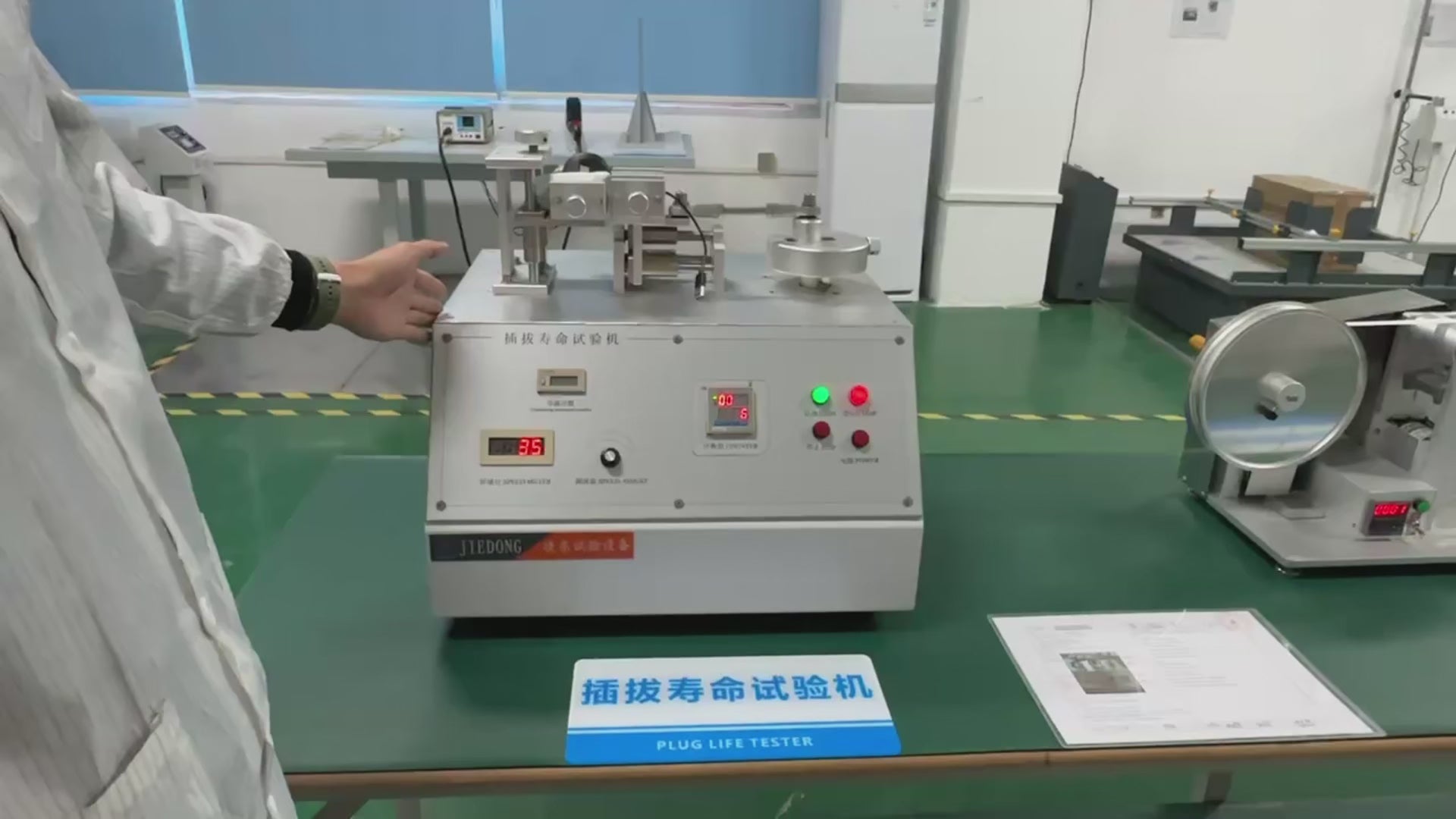
Mating Cycle Test Machine
This is our Mating Cycle Test Machine, designed to evaluate the durability of the charging port on each pair of earphones. Typically, we set the test to run for 5,000 insertion and removal cycles. After completing the test, we assess the electrical performance and charging functionality of the port to ensure they remain intact. Additionally, we inspect the charger's surface for any signs of wear. If there is minor wear but the charging function remains unaffected, the test is considered successful.
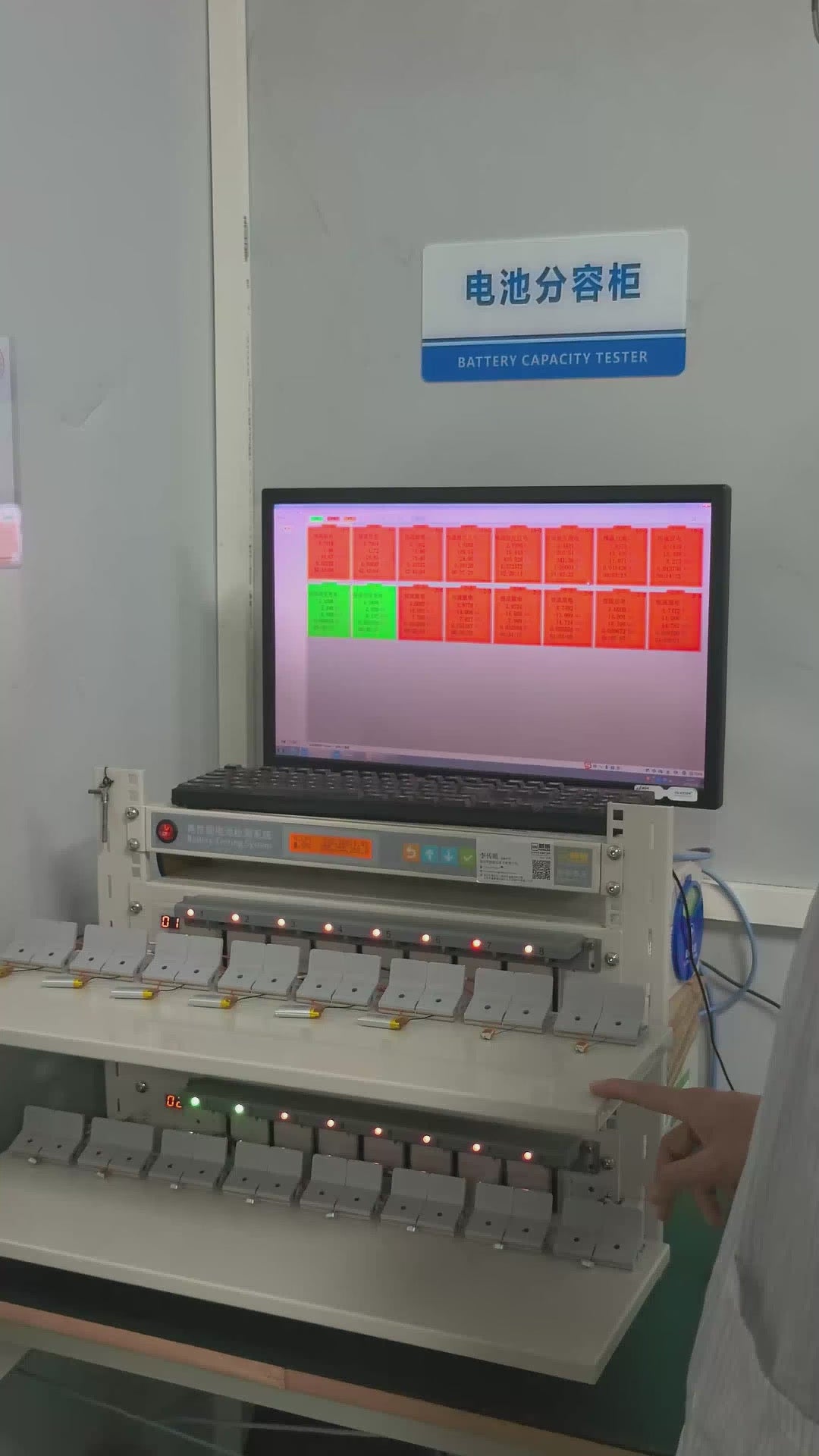
Battery Capacity Testing Cabinet
This is our battery capacity testing cabinet, used to perform battery capacity degradation tests. For each batch of orders, we randomly select a certain number of batteries for the capacity testing. The test typically involves 10 charge and discharge cycles to monitor if there is any capacity degradation. If the degradation is within 0.5 mAh, the battery is considered qualified; if it exceeds 1 mAh, the battery is deemed defective.
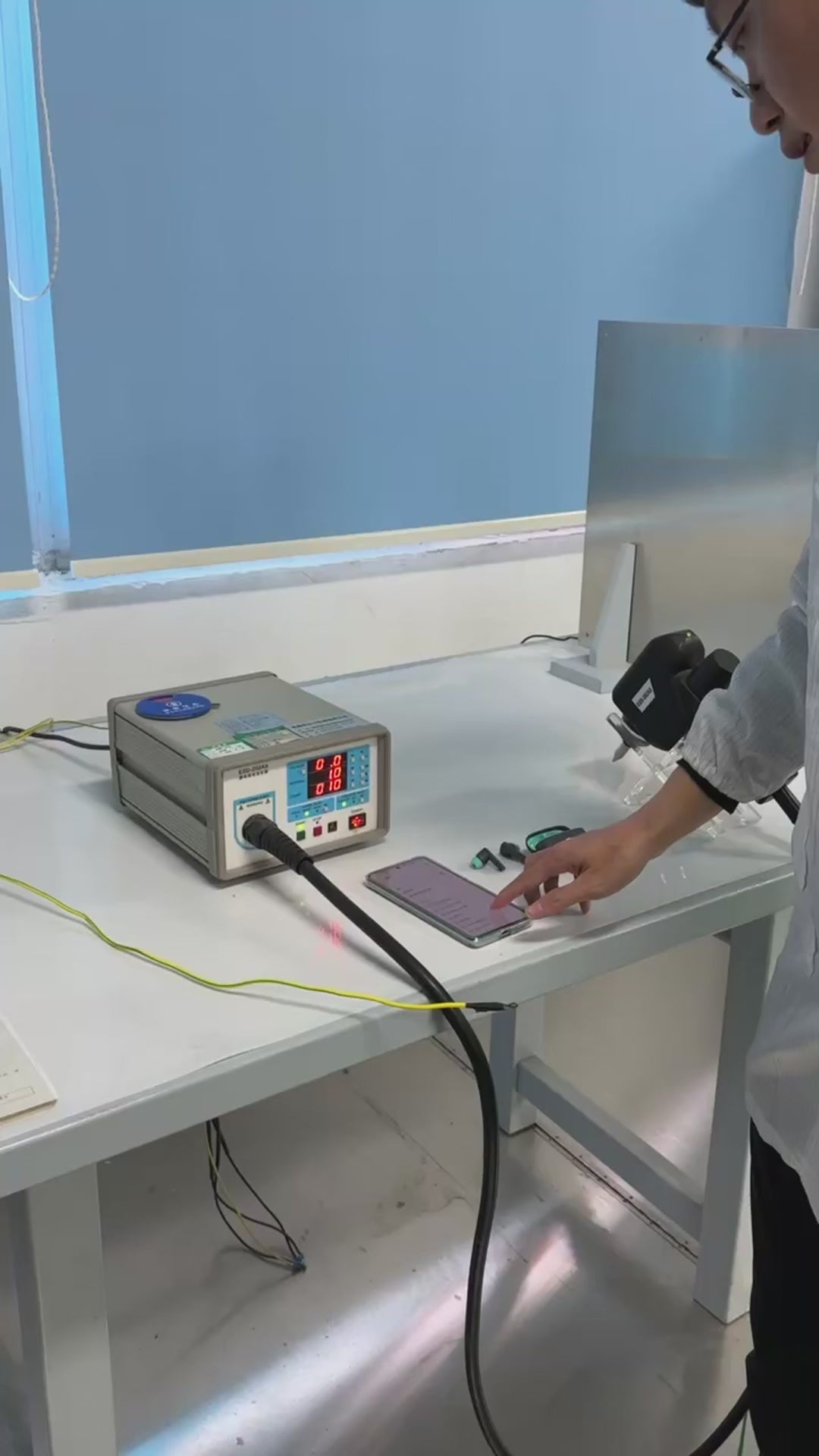
Headphone Electrostatic Tester
This is our electrostatic testing device for headphones. After completing the production of each batch of headphones, we perform electrostatic tests. The test includes contact discharge at ±6000 volts, and during the test, the headphones continue to play music. If the music does not pause and all functions remain normal during the electrostatic test, the headphones pass the test. The test involves 10 contact discharges for both positive and negative voltage. Afterward, we conduct a 6000-volt contact discharge test for the negative electrode, then switch to air discharge mode to perform a 10kV air discharge test. Throughout the entire process, if the headphones continue to play music without any interruptions or disconnections, they are considered to have passed the electrostatic test.
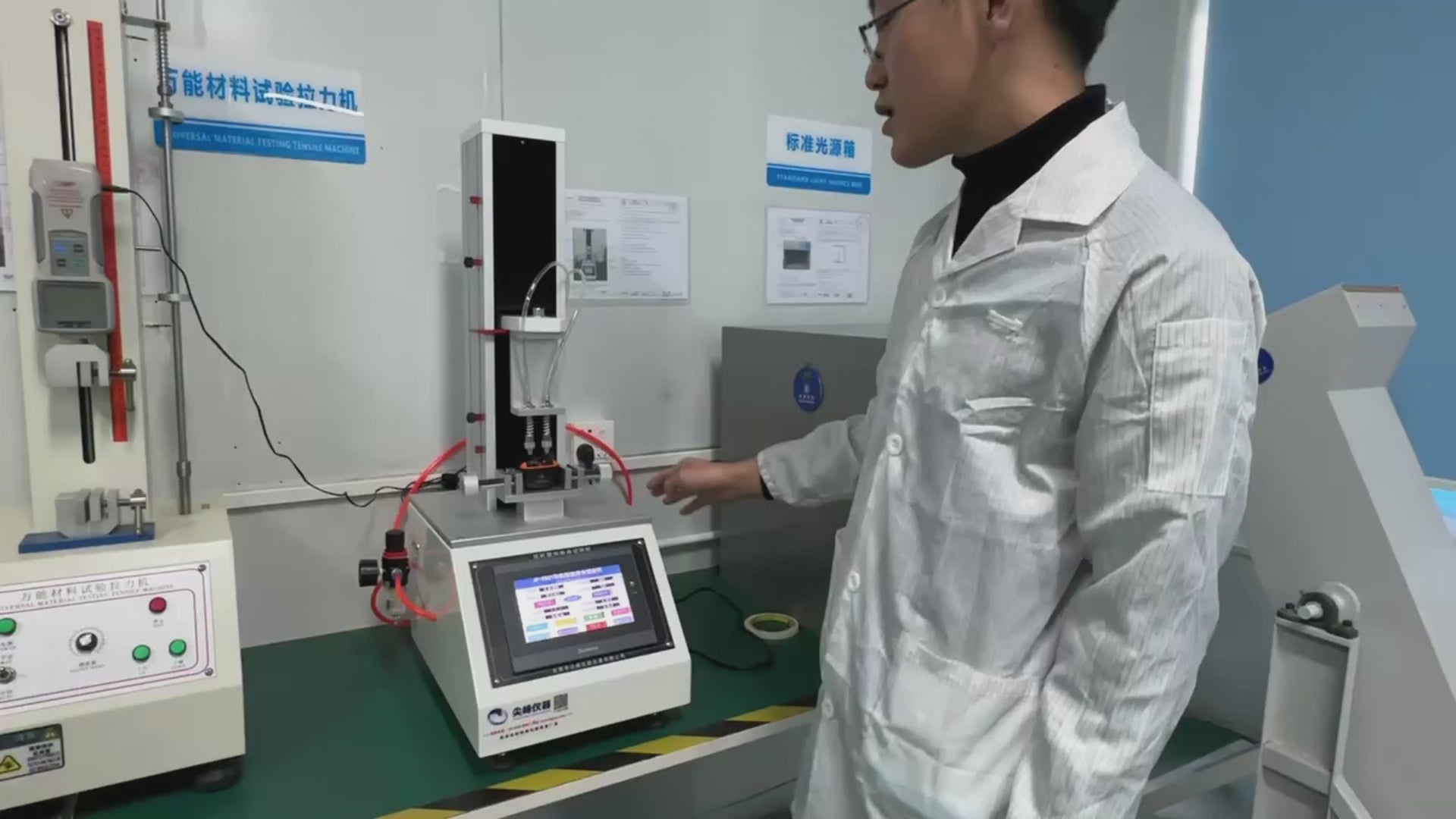
Headphone Placement and Removal Durability Test Machine
This is our earphone insertion and removal life test machine, used to test the lifespan of TWS earphones for each batch. During the test, we simulate the actions of picking up and placing the earphones, typically setting the test to 3,000 cycles. After completing the test, we check the charging functionality and other features to ensure they are working properly. If the earphones exhibit no functional issues after the test, they are deemed qualified.
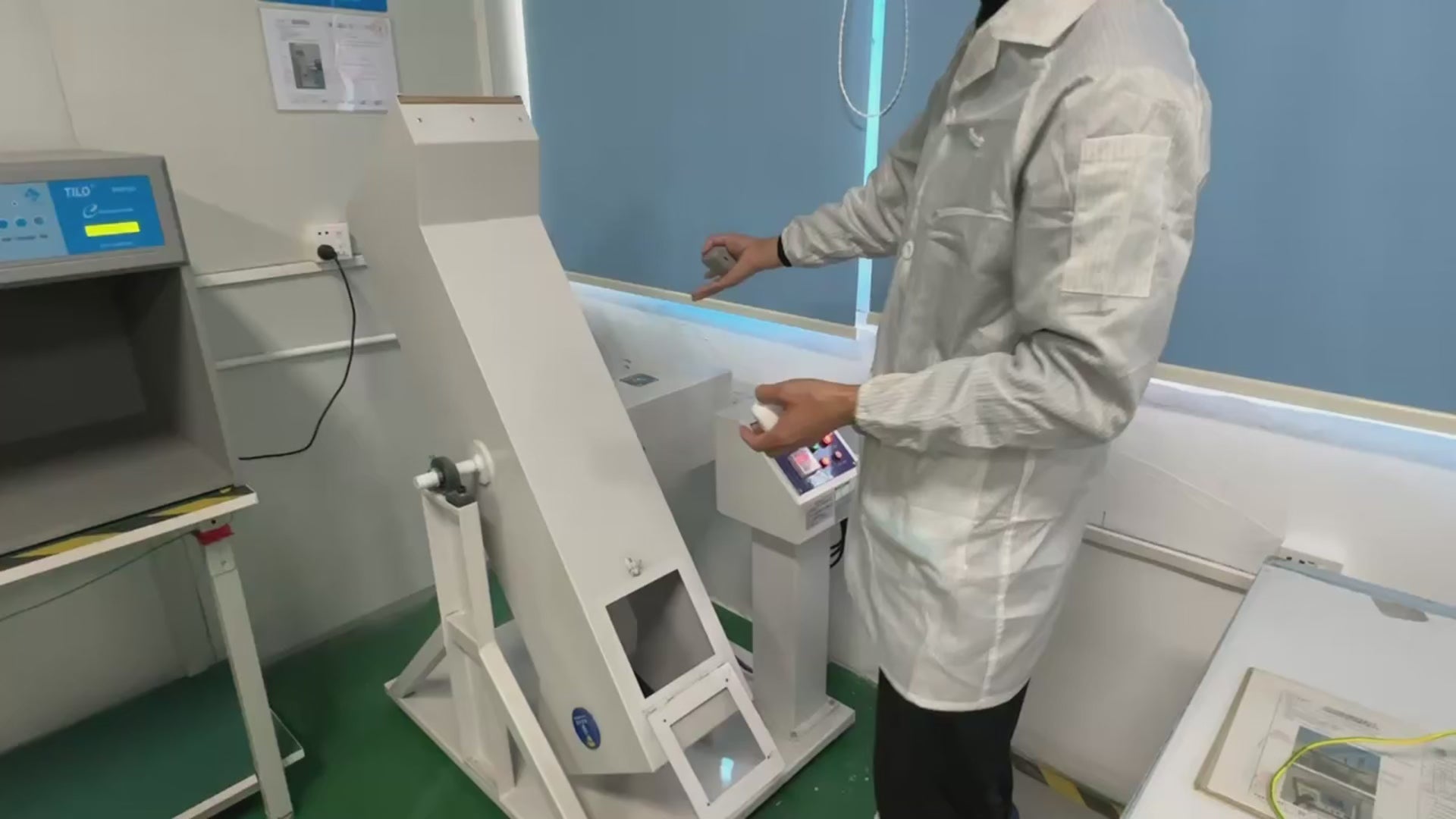
Tumble Drop Test
This is our drum drop testing machine. After completing a batch of headphones or orders, we randomly select a portion of the headphones for drum drop testing. During the test, the headphones are placed inside the drum, the lid is closed, and the test is initiated to simulate a drop scenario. The drop height is 1.5 meters, and the headphones undergo 50 drops. After completing 50 drops, we remove the headphones and perform a thorough inspection of their appearance to ensure there is no visible damage, and that all functions and the overall structure of the headphones remain intact.

Sweat Immersion Test
This is our simulated artificial sweat with a pH value of 4.7, used for sweat immersion testing. During the test, we pour the sweat into a container and submerge the product in it for the immersion test. Typically, our products can withstand at least one hour of sweat immersion without any performance degradation. During the test, we keep the device connected and play music to monitor its functionality. The entire test lasts for over an hour, during which we observe whether the audio continues to play normally, ensuring that the device's performance remains stable after exposure to the sweat.
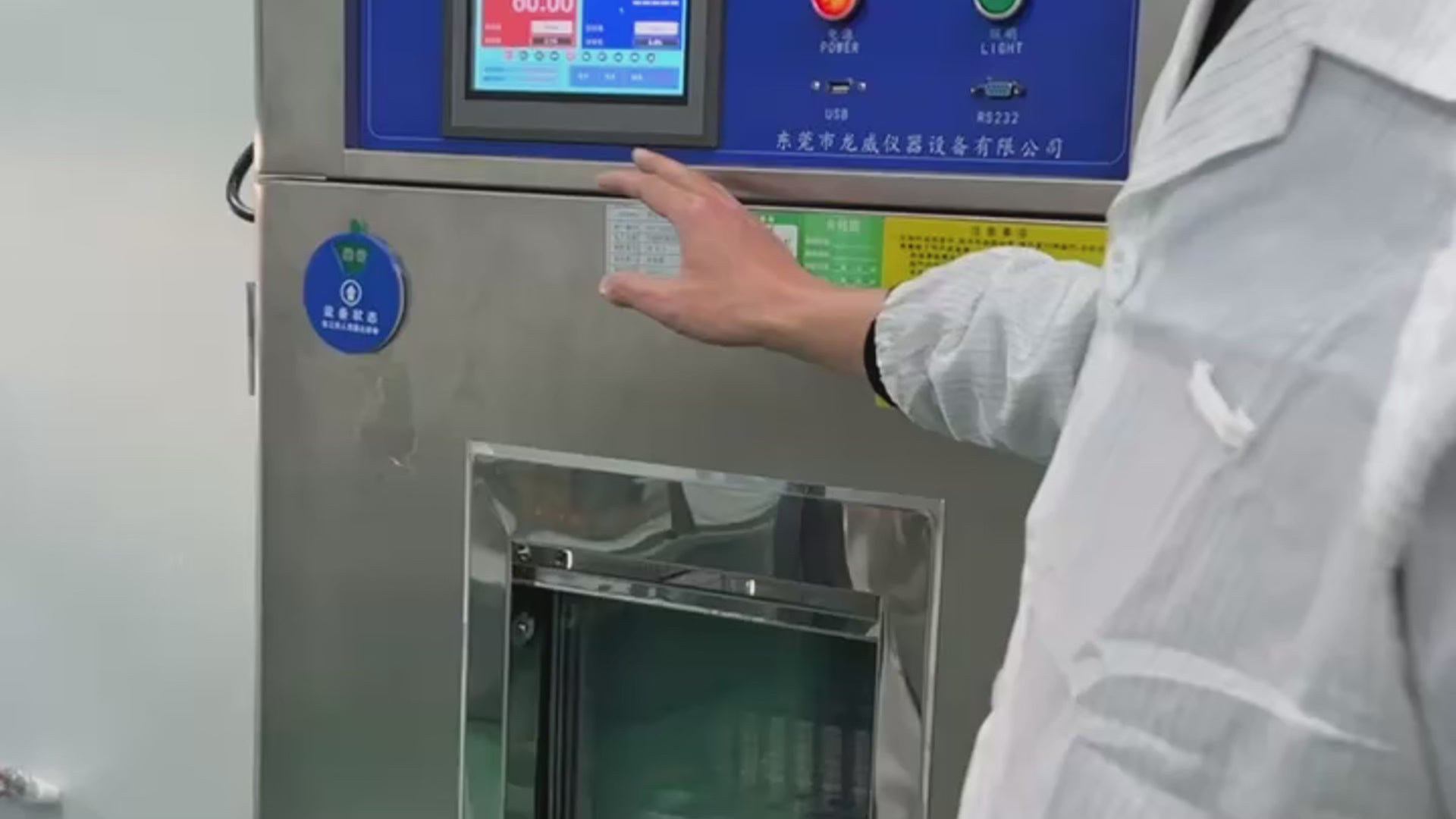
Constant Temperature and Humidity Test Chamber
This is our temperature and humidity testing chamber, used to conduct temperature shock, high-temperature operation, and low-temperature operation tests for products such as headphones. During the test, the device is exposed to an environment with a high temperature of 60°C and humidity of 85%, followed by a low-temperature test at -20°C. The entire test usually lasts for 48 hours. After the test is completed, we remove the headphones and check their functionality to ensure they perform as expected.
This temperature and humidity testing chamber is primarily used for high-temperature reliability testing of batteries. After conducting a 48-hour test at 60°C, we perform a thorough examination of the battery’s communication functions and capacity, ensuring that it maintains optimal performance even under extreme temperature and humidity conditions.
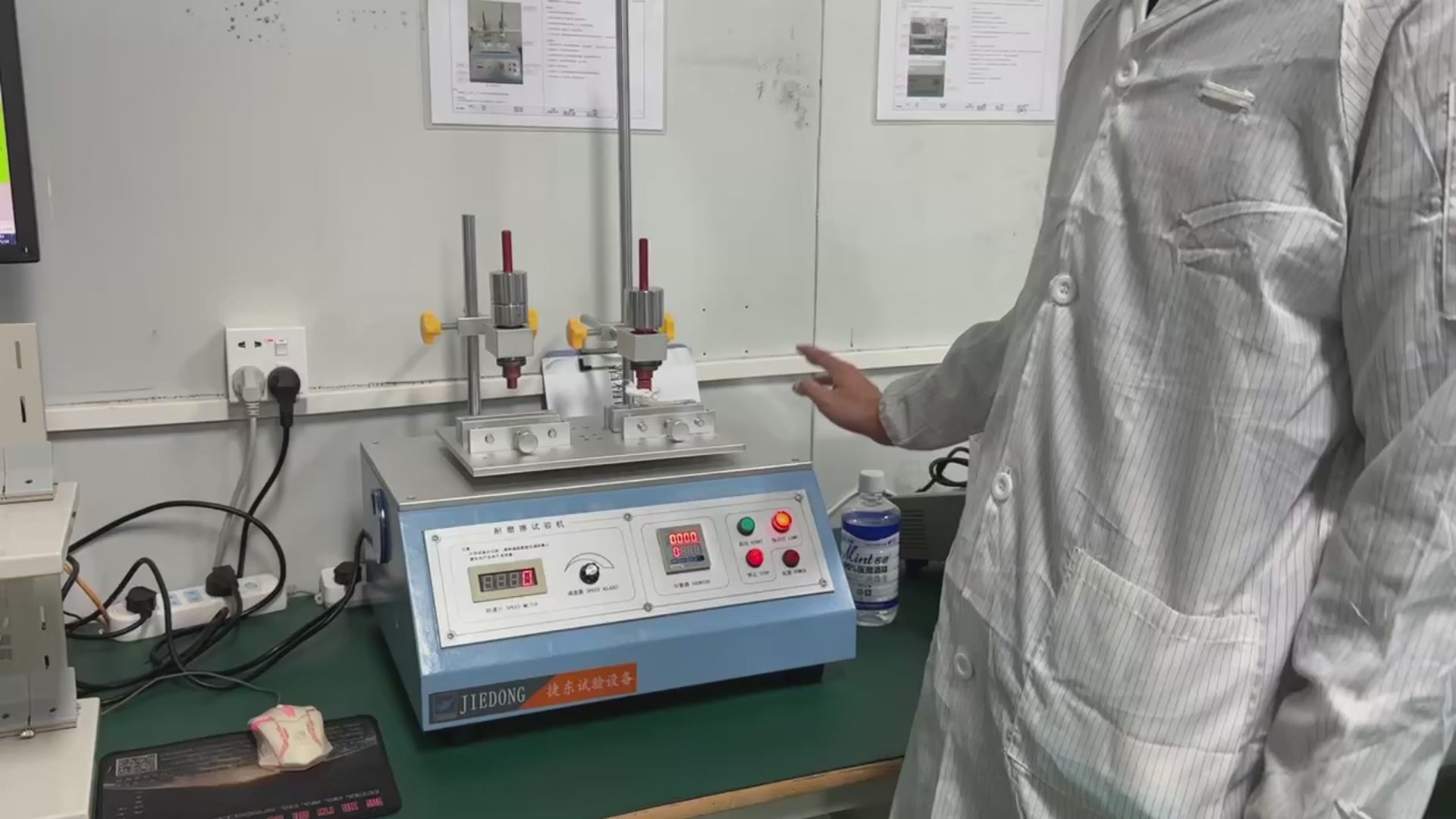
Alcohol Rubber Abrasion Tester
This is our alcohol abrasion resistance testing machine, used to assess the reliability of the logos and silkscreen prints on the outer shell of each batch of headphones. During the test, we use 95% alcohol and apply a 500g weight to press on the silkscreened area. Once the machine is started, it performs an abrasion test on the silkscreen region. Typically, we conduct 30 cycles of testing. If no paint peeling, wear, or base layer exposure occurs in the silkscreen area, the product is considered qualified. After the test, we inspect the headphones’ silkscreen, ensuring that the logo and print are intact and free from any missing or blurred areas.
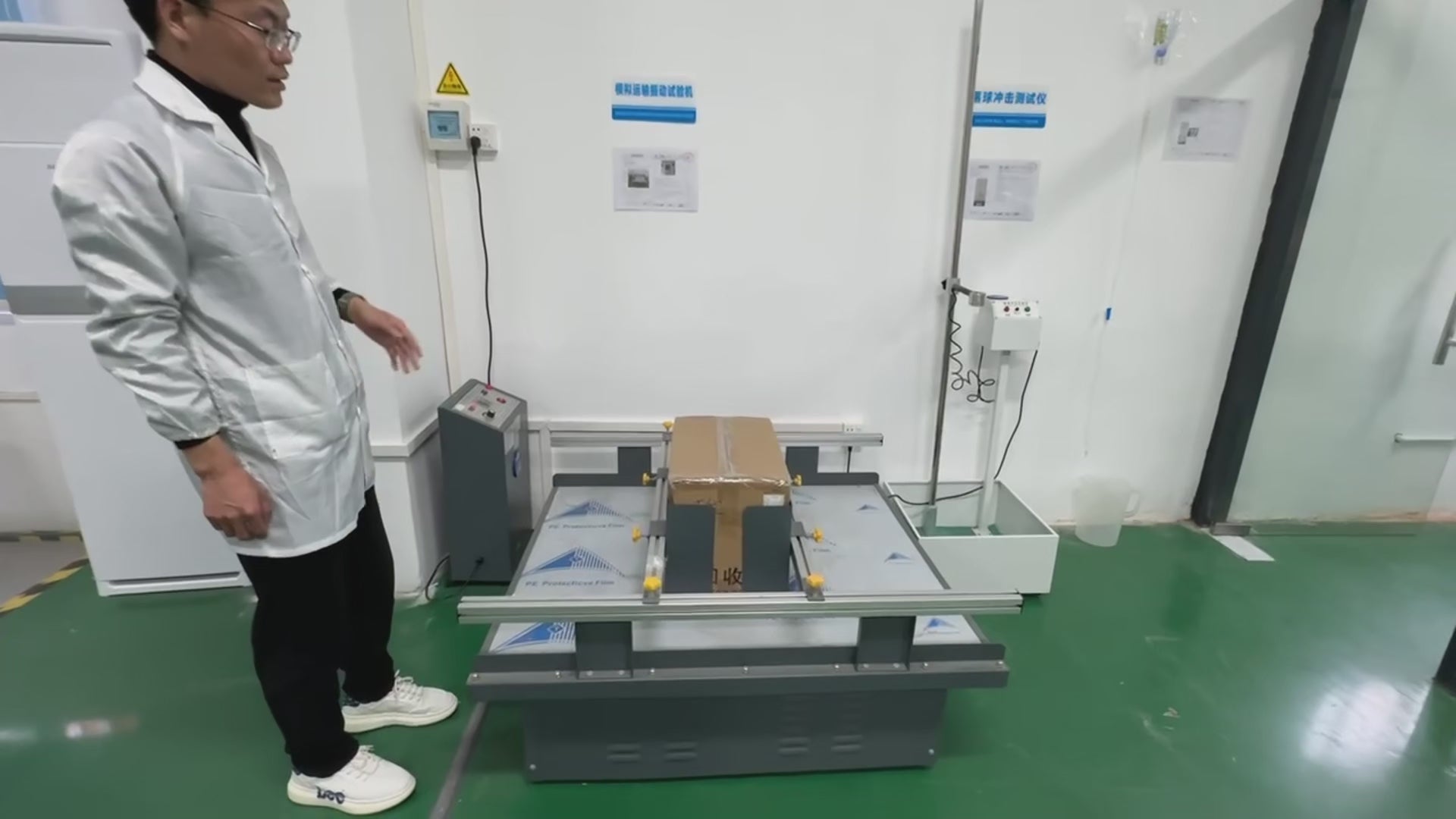
Simulated Transportation Vibration Tester
This is our transportation vibration testing machine, primarily used to simulate the vibrations that may occur during shipping. After the products are packaged, we place them in the machine for a one-hour vibration test. Once the test is completed, we inspect the products inside the packaging to ensure that they have not been damaged by the vibrations and are still fully functional.
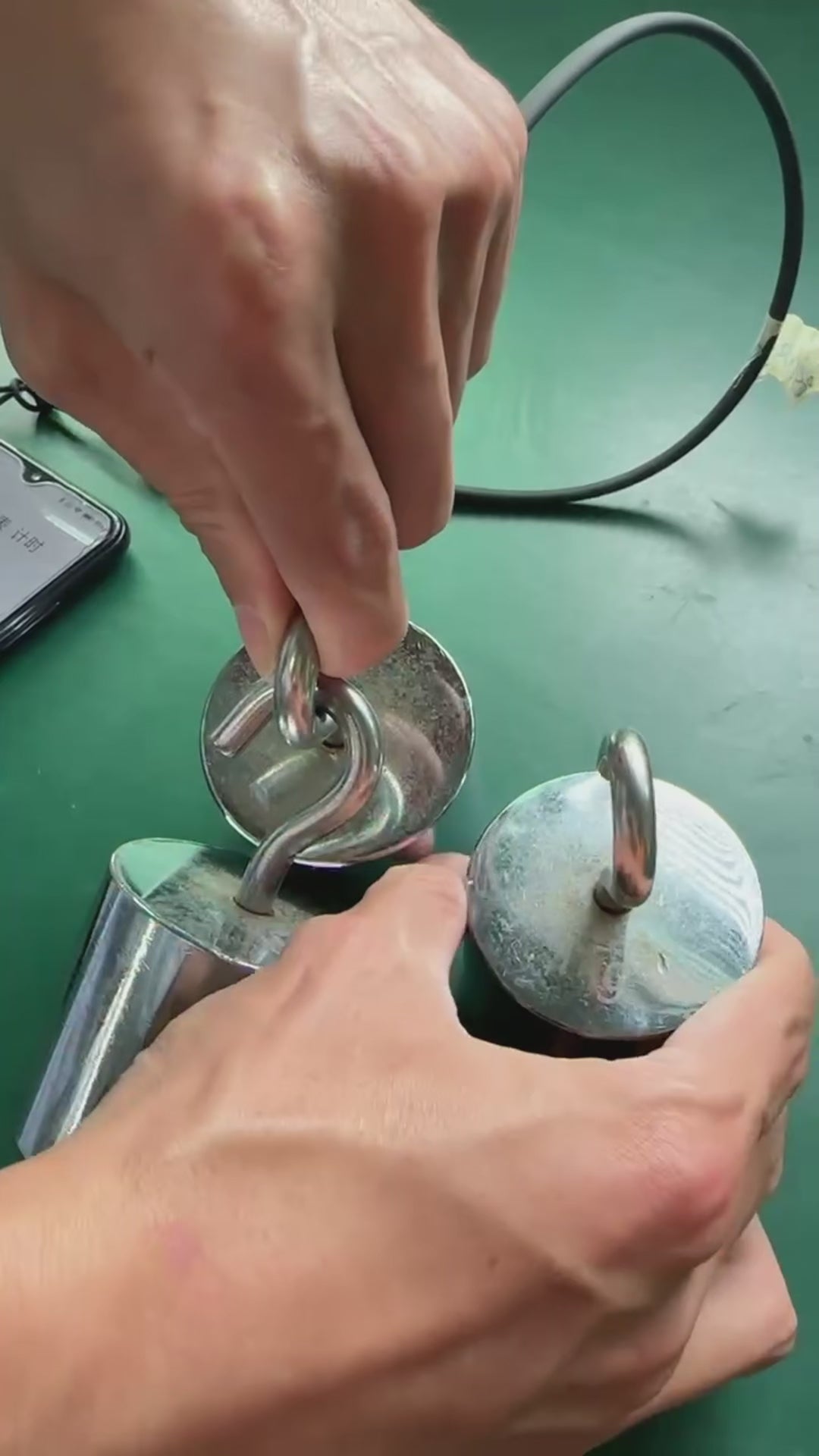
Cable Tensile Strength Test
This is our wire tension testing equipment. During the test, we suspend a 3 kg weight and hold it for 60 seconds. After the test, we inspect the wire to ensure it remains intact under tension, with no signs of breakage or visible damage.
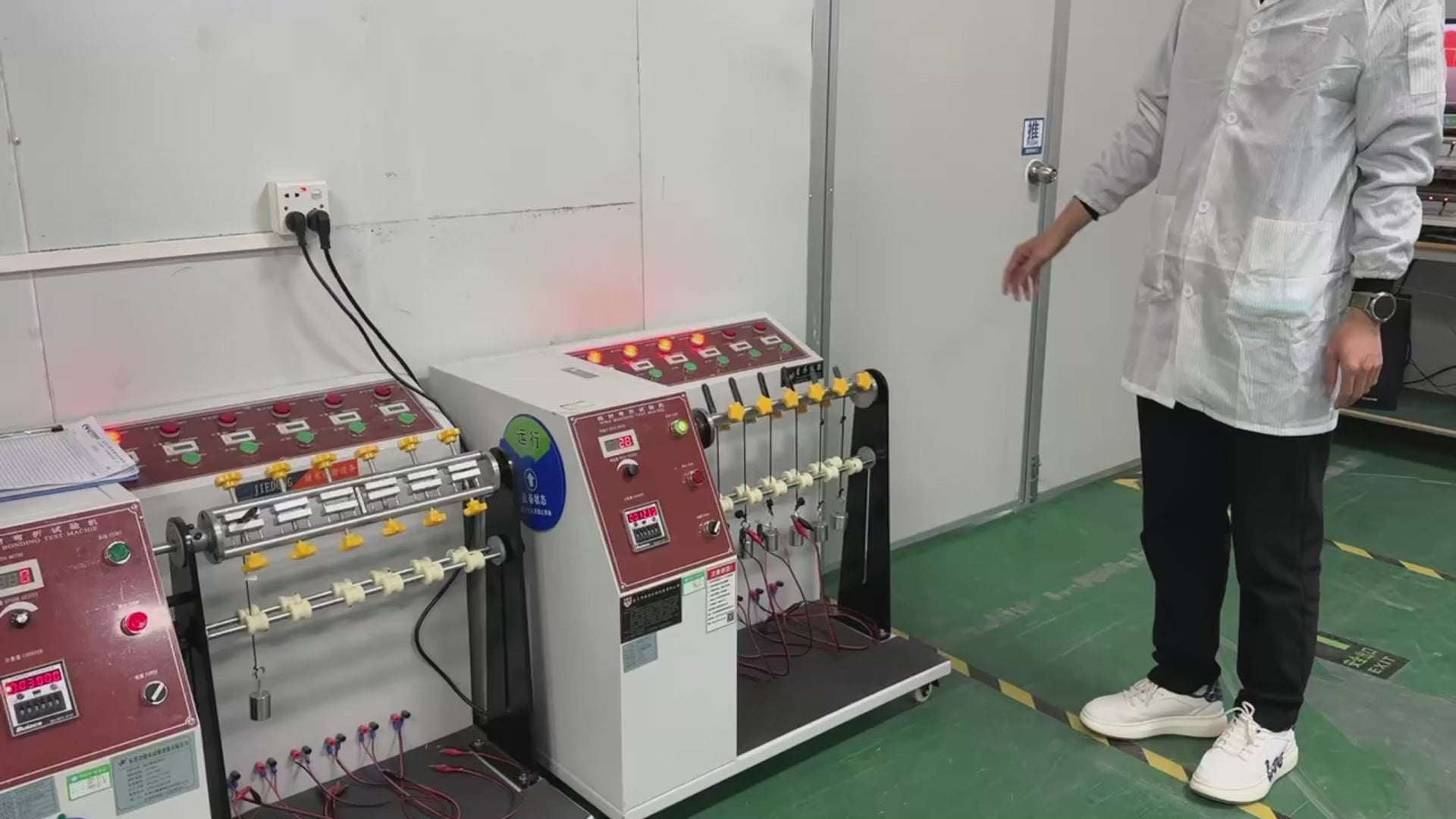
Cable Bending Test Machine
This is our wire bending test machine, used for swing testing, primarily for assessing the reliability of neckband and sports-style headphones. During the test, we connect the wire to the device and set the bending cycle to 30,000 times. If the wire maintains proper connectivity and functionality after 30,000 bends, it is considered passed. If the wire fails to meet the test conditions during the process, the machine will automatically stop. Once the test reaches the set number of cycles, the wire is judged to have passed the test.
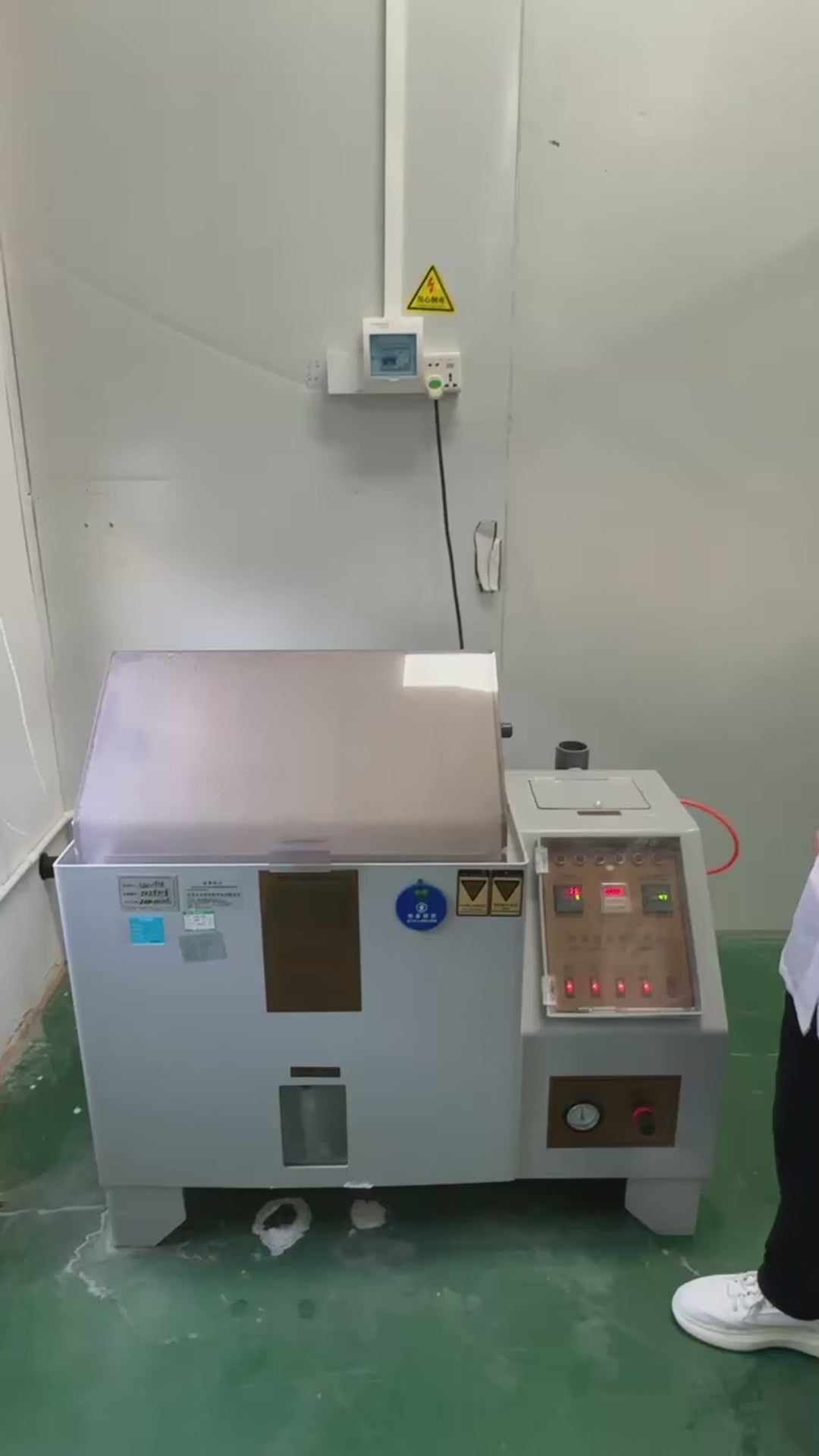
Salt Spray Testing Chamber
This is our salt spray testing chamber, used to perform salt corrosion tests on products. During the test, we expose the product to a 5% sodium chloride solution for 48 hours of salt mist spraying. After the test is completed, we wipe and clean the surface of the headphones to remove any remaining salt mist, and then check the functionality of the headphones. This test allows us to evaluate the corrosion resistance of the headphones when exposed to long-term salt mist conditions, ensuring that both their appearance and functionality remain unaffected.
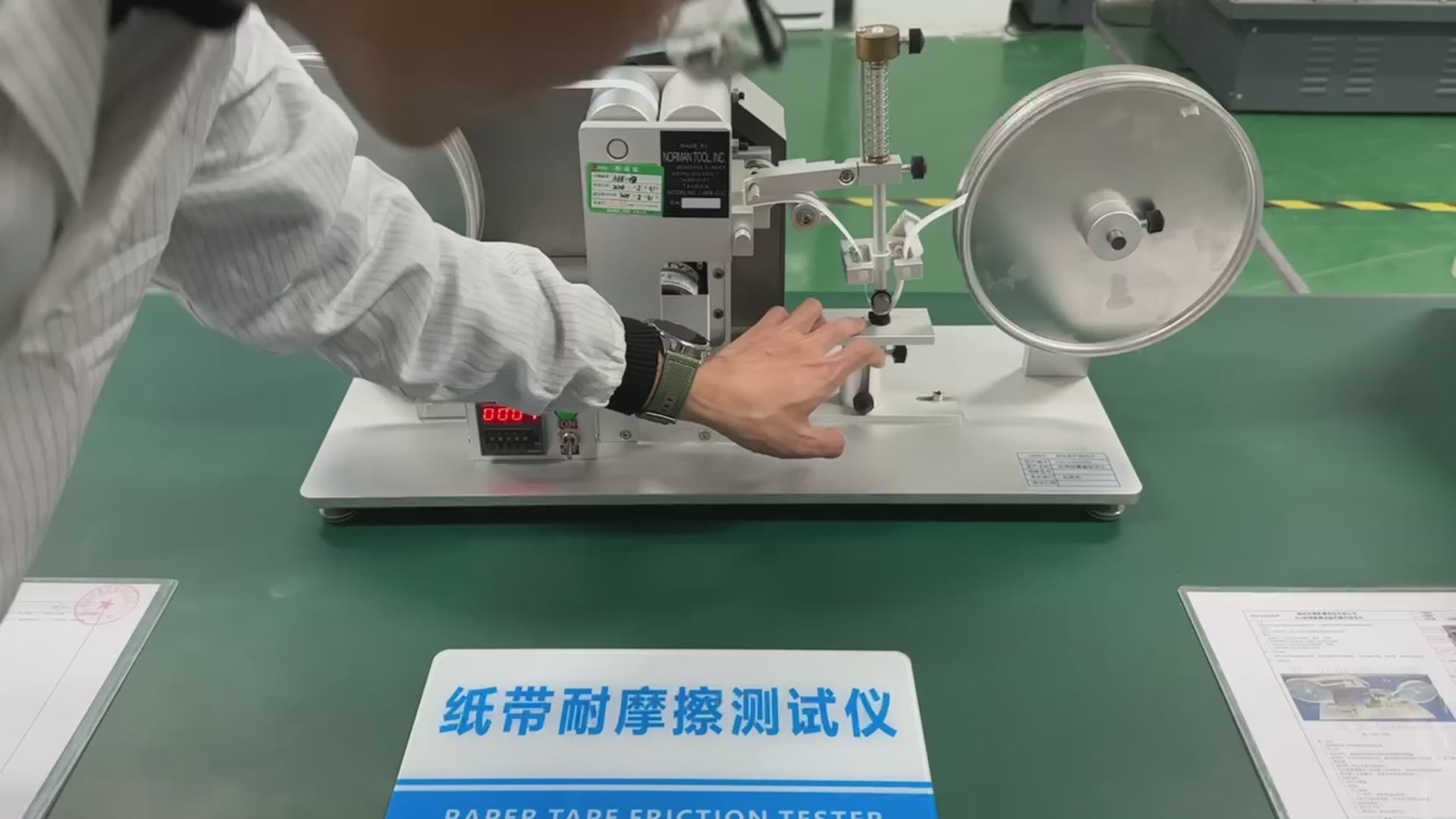
Paper Tape Abrasion Testing Machine
This is our paper tape abrasion testing machine, mainly used to assess the durability of logos and silkscreen prints on products. During the test, we fix the product in the designated position and apply 95% alcohol and a 500g weight for the abrasion test. After completing the test, we inspect the silkscreen area to ensure the print remains intact, with no peeling, base exposure, or missing parts. If the print remains in good condition, the product is considered qualified.